Schlaue Algorithmen bringen Industrie 4.0 ans Laufen

Seit Mitte des letzten Jahrhunderts baut die Firma Christian Mayr GmbH & Co. KG in Mauerstetten bei Kaufbeuren moderne Antriebskomponenten, unter anderem Kupplungen und Bremsen. Bild: Chr. Mayr GmbH + Co KG
Über das intelligente Nutzen von Sensordaten lassen sich für Anwender interessante Ergebnisse ablesen – wenn „schlaue“ Algorithmen die passenden Ergebnisse, wie zum Beispiel den Zeitpunkt der notwendigen Wartung prognostizieren. Bei der Mayr GmbH + Co. KG ist im Bereich der Antriebstechnik ein Industrie 4.0-Projekt realisiert worden.
Der Wunsch, wichtige Informationen aus der Umwelt automatisch zu erfassen und zu kommunizieren, besteht schon lange. Ein sehr populäres Beispiel dafür sind die vielen digitalen Wetterstationen, die – ohne menschliches Zutun – allein durch intelligente Vernetzung und Verknüpfung sowohl die Daten zur aktuellen Wetterlage liefern als auch eine Prognoserechnung zulassen. Seit Kevin Ashton, ein Technologie-Pionier am Massachusetts Institute of Technology (MIT) 1999 erstmals den Begriff „Internet of Things“ verwendet hat, ist ein regelrechter Run auf automatisch und permanent sprudelnde Datenquellen für das Internet der Dinge ausgebrochen.
Eine dieser Quellen sitzt da, wo etwas, zum Beispiel Maschinen oder Aufzüge, mit Motorkraft angetrieben wird, und wo das dabei erzeugte Drehmoment gemessen, überwacht und gesteuert werden muss, also in Hebewerkzeugen, Förderbändern oder Prüfständen. Alle diese Maschinen müssen nicht nur angetrieben, gesteuert und überwacht, sondern auch gewartet werden.
Solange die Welt überwiegend „analog“ dachte und handelte, schalteten die Wartungstechniker diese Maschinen in zuvor festgelegten Zeitabständen ab. Dann wurden Motoren, Kupplungen und Bremsen überprüft und ggf. ausgetauscht. Dabei kam es natürlich vor, dass einige Bauteile vorbeugend ausgewechselt wurden, obwohl sie eigentlich noch völlig in Ordnung waren und bedenkenlos weiter genutzt werden hätten können.
Industrie 4.0 trifft das Allgäu
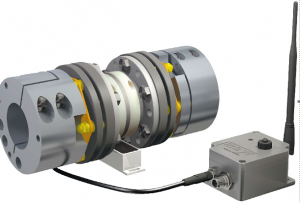
Seit Mitte des letzten Jahrhunderts baut die Firma Christian Mayr GmbH & Co. KG in Mauerstetten bei Kaufbeuren moderne Antriebskomponenten, unter anderem Kupplungen und Bremsen. Der Trend „Industrie 4.0“ erreichte auch das Allgäu, und die Entwicklungsingenieure der Firma Mayr begannen vor einigen Jahren nach Digitalisierungsmöglichkeiten zu suchen. Und weil auch Sicherheitskupplungen und -bremsen zur Angebotspalette des Unternehmens gehören, war das visionäre Ziel, Komponenten für das „Condition Monitoring“ zu bauen, also für die Zustandsüberwachung. Diese neue Funktion sollte künftig bei Kupplungen und Bremsen zwei Aufgaben erfüllen: mehr Sicherheit und Steigerung der Effizienz.
Die Neuorientierung an der digitalen Welt eröffnete dem Unternehmen neue Horizonte – aber auch neue Märkte. Viele Kunden waren von den zusätzlichen Möglichkeiten, die sich durch die Ausgabe digitaler Daten aus den Komponenten ergeben, so begeistert, dass sie den Einsatzzweck bis heute geheim halten, weil sie darin einen Konkurrenzvorsprung sehen.
Wenige Daten genügen
Zunächst sollte für das „Condition Monitoring“ der Kupplungen die Laufzeit, die Anzahl der Einschaltintervalle und Überlastzustände erfasst und gespeichert werden. Was man mit diesen Daten machen kann, zeigen die folgenden Beispiele.
Beispiel 1: Die bisher gebauten Sicherheitssysteme waren im Vergleich zu digital gesteuerten etwas unpräzise. Für ein verlässliches und schnell reagierendes Sicherheitssystem, zum Beispiel für eine Notabschaltung, braucht man Sensordaten in Echtzeit. Außerdem könnten die gespeicherten Daten anschließend zur Aufklärung der Schadensursache beitragen.
Beispiel 2: Die größte Kosteneinsparung im Life Cycle einer Maschine ist die Erhöhung der Lebensdauer wichtiger Maschinenelemente. Ein Condition Monitoring mit exzellenter Sensorik und geeigneter Messdatenerfassung könnte eine gute Basis dafür sein. Allerdings müssten die Daten in digitaler Form vorliegen. Die Ingenieure der Firma Mayr haben die von ihren Komponenten gelieferten Daten auch noch sichtbar gemacht. Deren Auswertung, Analyse und gegebenenfalls daraus Schlussfolgerunen zu ziehen, sehen sie als Aufgabe des Anwenders an.
Schlaue Algorithmen sind gefragt
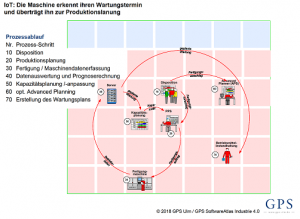
Einen weiteren Nutzen der Sensordaten kann der Anwender aus einer Datenanalyse erreichen, wenn „schlaue“ Algorithmen den Zeitpunkt der notwendigen Wartung prognostizieren. Dazu sind natürlich anlagenspezifische Kenntnisse erforderlich. Die dabei erzielbaren Erfolge sind vielfältig: Durch den Blick in die Zukunft können früher „unvorhersehbare“ Maschinenschäden vermieden werden. Das wiederum ergibt einen optimalen Schutz für die Maschine und die Umwelt sowie die bestmögliche Nutzung der Lebensdauer der Komponenten.
Die Mehrkosten für entsprechende Sensorik an sicherheitsrelevanten Bauteilen werden durch eine genauere und individuelle Abnutzungsbetrachtung der einzelnen Komponenten und die damit einhergehende Nutzenmaximierung kompensiert. Viele Maschinenhersteller beweisen heute schon diesen unternehmerischen Weitblick und setzten entsprechende Technik ein. Denn zufriedene Kunden haben Produkte, die funktionieren und nicht durch unplanmäßige Stillstände die Produktion oder den Betrieb lahmlegen.
Natürlich denkt man bei Mayr auch an die mögliche Vernetzung der Daten. Allerdings sind die heutigen Planungssysteme, zum Beispiel ERP-Systeme noch zu „statisch“. Das heißt sie gehen immer von der 100-prozentigen Verfügbarkeit der Maschinen aus. (Geplante) Wartungs- oder Stillstandszeiten müssen manuell in diese Systeme eingetragen werden.
In Zukunft könnte die Überwachung der Antriebsteile signalisieren, dass in so und so viel Betriebsstunden der Maschine eine Wartung erforderlich ist und ein weiterer – ebenfalls schlauer – Algorithmus könnte die passende Lücke im Produktionsplan finden, in der die Wartung ohne Produktionsausfall durchgeführt werden könnte.
(Werner Schmid und Andreas Wachter, GPS Gesellschaft zur Prüfung von Software mbH, Ulm)
Hier geht es zu Chr. Mayr GmbH + Co.